
Visitors can get hands-on experience printing and making books in classes offered at the museum. Photo by Taku Yaginuma / Special to The Yomiuri ShimbunĪn automatic casting machine, which mass produces types, and a threading machine used to bind books are also on display at the museum. Since a new matrix had to be created for each font size and typeface, there are said to be as many as 300,000 matrices at the main factory, which printed a variety of books and magazines. As a large pen-like component traced the original letters, an engraver moved in tandem. A machine called a letterpress pantograph was then used to reduce the size of the letters and inscribe them into a matrix, which served as a type template.
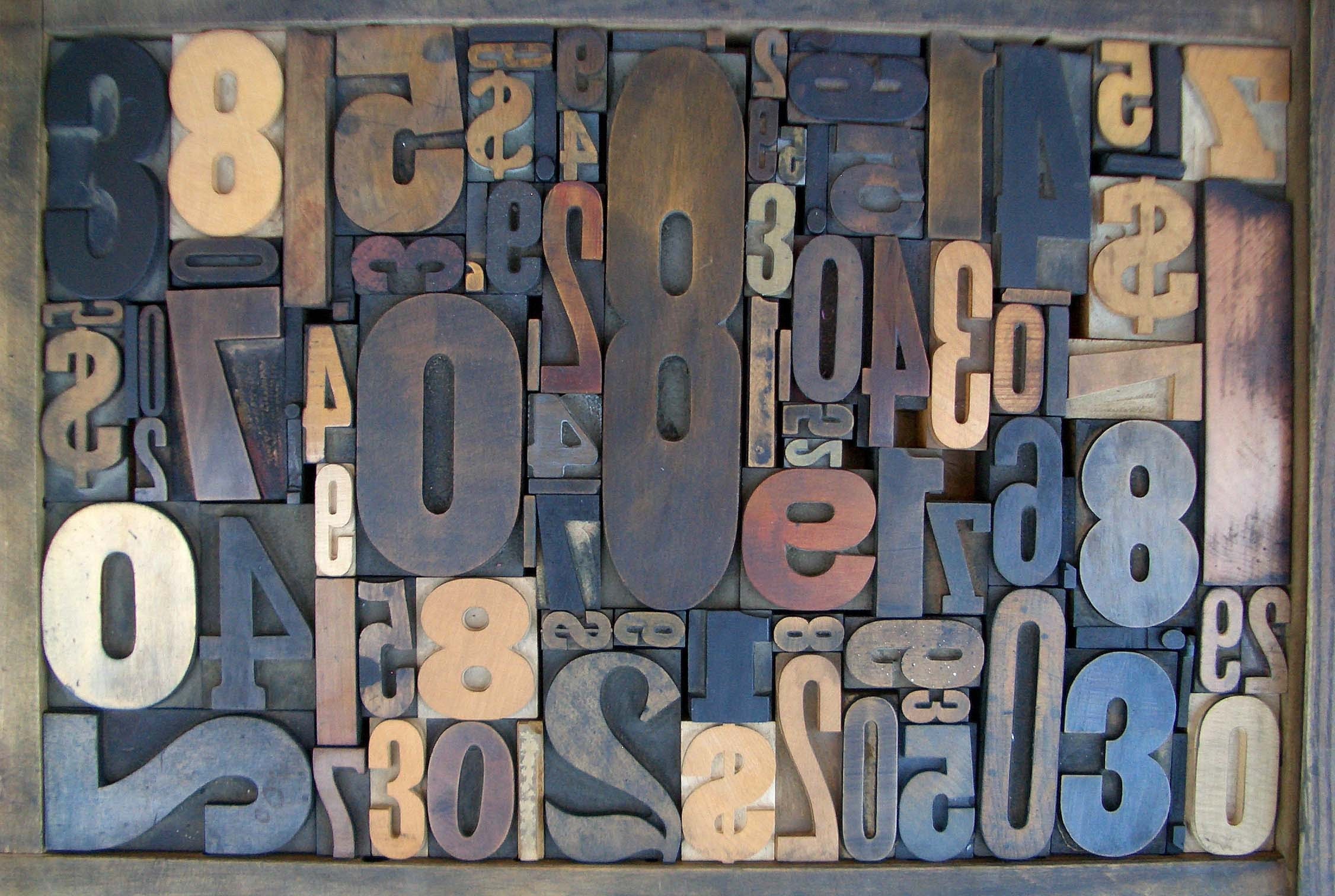
The letters were first written by hand on a piece of paper about the size of a playing card. Types used to be produced at the factory as well. Photo by Taku Yaginuma / Special to The Yomiuri Shimbun The entire process is shown in a video at the museum. Some of the metal pieces were interu, which created the spaces between the lines, and kuwata, which filled the blank spaces at the end of each sentence and other sections. The plate makers would also insert metal pieces among the types. Letterpress plate makers used to quickly find types they needed from shelves, or uma, while looking at a manuscript, and then arrange them inside the frame by hand. One could never tire of looking at the claws on the cylinder as it grips the printed page. Then, the freshly inked type passes under the impression cylinder to print onto a sheet of paper. The type bed moves backward and forward, pressing ink onto the type. One of the main items on display at the museum is a flatbed letterpress machine that was used during the early Showa era (1926-89). Famous publications such as the weekly magazine Shukan Shincho and the Kojien dictionary used to be printed at the factory.

The museum opened last year at the former site of Dai Nippon Printing’s main factory to show the history and appeal of the letterpress.

The museum also displays working machines. The Ichigaya Letterpress Factory, a museum located next to Dai Nippon Printing Co.’s headquarters in Shinjuku Ward, Tokyo, introduces visitors to the process of letterpress printing from type production to printing and bookbinding. Before electronic editing became the norm, letterpress printing was a technique that was essential to the publishing industry. Letterpress printing is a process that requires individual types, which are letters that are sometimes the size of a grain of rice, to be placed in a frame by hand to form words and sentences. Photo by Taku Yaginuma / Special to The Yomiuri Shimbunīy Kazuyoshi Nakaya / Yomiiuri Shimbun Staff Writer
